Are you tired of battling with stubborn camlock fittings? Do leaks and corrosion keep you up at night? You’re not alone in this struggle! Camlock fittings are the unsung heroes of industrial fluid transfer, but they can also be a major headache when things go wrong. Don’t worry, though – we’ve got your back. Camlock Fitting Woes? Your Ultimate Troubleshooting Guide for Industrial Fluid Transfer.
The ABCs of Camlock Fittings: Your Crash Course in troubleshooting, maintenance, and mastery.
Fluid Connection Mastery
Before we tackle the nitty-gritty of troubleshooting, let’s get acquainted with these vital components. Camlock fittings, also known as cam and groove couplings, are quick-connect fittings used extensively in industrial fluid transfer applications. They consist of two main parts: a male adapter (plug) and a female coupler (socket). The “cam” refers to the lever arms on the female part that lock the two pieces together.
Camlocks work by inserting the male adapter into the female coupler and then rotating the cam arms to create a secure, leak-proof seal. This design allows for quick and easy connections and disconnections without the need for tools – a major time-saver in industrial settings.
In the USA, Camlock fittings are ubiquitous across various industries, including:
- Chemical processing
- Food and beverage production
- Petroleum and oil transfer
- Agricultural irrigation
- Wastewater management
Now that we’ve covered the basics, let’s dive into the most common camlock conundrums and how to solve them.
Top 7 Camlock Conundrums (and How to Kick ‘Em to the Curb)
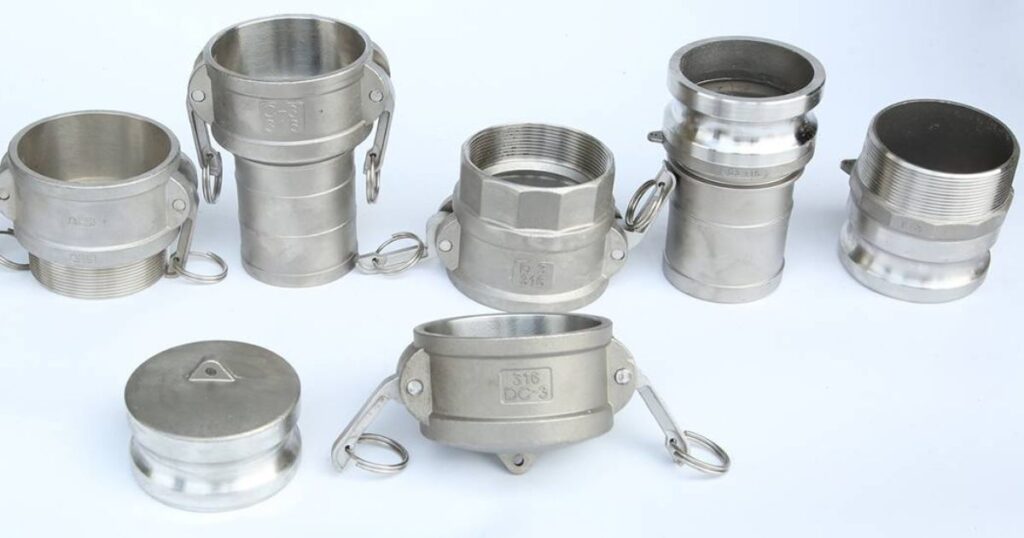
1. Leaky Connections: When Your Fitting Can’t Hold Its Water (or Oil, or Chemicals…)
There’s nothing quite as frustrating as a leaky camlock fitting. Not only does it waste valuable fluids, but it can also create safety hazards and environmental concerns. Here are the most common causes of leaks and how to address them:
- Worn or damaged gaskets: Over time, the gaskets that create the seal between the male and female parts can wear out or become damaged. Inspect your gaskets regularly and replace them at the first sign of wear.
- Improper alignment: If the male and female parts aren’t properly aligned when connected, it can lead to leaks. Always ensure a straight, even connection.
- Debris in the fitting: Even small particles can interfere with the seal. Clean your fittings thoroughly before each use.
Quick fix: For minor leaks, try applying a food-grade silicone lubricant to the gasket. This can sometimes provide a temporary seal until you can replace the gasket. Camlock Fitting Woes? Your Ultimate Troubleshooting Guide for Industrial Fluid Transfer.
2. Stubborn Couplings: Wrestling with Connections and Disconnections
Ever feel like you need superhuman strength to connect or disconnect your clocks? Here’s how to make your life easier:
- Lubricate regularly: Apply a thin layer of food-grade silicone lubricant to the cam arms and locking grooves. This reduces friction and makes operation smoother.
- Check for misalignment: Ensure the male and female parts are perfectly aligned before attempting to connect them.
- Inspect for damage: Look for bent cam arms or damaged locking grooves that could be causing resistance.
Pro tip: Invest in a camlock fitting wrench. This specialized tool provides extra leverage for stubborn connections without damaging the fitting.
3. Rust Monsters Attack: Battling Corrosion and Rust
Corrosion is the arch-nemesis of camlock fittings, especially in harsh industrial environments. Here’s how to keep the rust monsters at bay:
- Choose the right material: For corrosive environments, opt for stainless steel or specialized alloy fittings.
- Regular cleaning: After each use, clean your fittings with warm, soapy water and dry thoroughly.
- Apply protective coatings: For added protection, consider using food-grade anti-corrosion sprays on your fittings.
Case study: A food processing plant in California was experiencing frequent camlock failures due to corrosion. By switching to 316 stainless steel fittings and implementing a rigorous cleaning routine, they reduced fitting replacements by 75% over two years.
4. Worn-out Warriors: Dealing with Seal Surface Fatigue
Even the toughest camlock fittings can’t escape the ravages of time and use. Here’s how to spot and deal with wear and tear:
- Look for scoring or pitting on the sealing surfaces.
- Check for excessive play in the cam arms.
- Test the spring tension in the cam arms – they should snap back firmly when released.
To extend the life of your seals:
- Rotate your stock of fittings to distribute wear evenly
- Use lubricants designed for your specific application
- Store fittings properly when not in use (more on that later!)
5. Storage Snafus: Keeping Your Camlocks Happy Between Gigs
Proper storage is crucial for maintaining your camlock fittings. Follow these tips to keep them in top shape:
- Store in a cool, dry place away from direct sunlight
- Use dust caps or plugs to prevent contamination
- Hang fittings vertically to prevent distortion of gaskets
Pre-use inspection checklist:
- [ ] Check for visible damage or corrosion
- [ ] Ensure gaskets are intact and properly seated
- [ ] Verify cam arms move freely and lock securely
- [ ] Look for any debris or contamination in the fitting
6. Hulk-Mode Mishaps: The Perils of Over-Tightening
While it’s tempting to crank those cam arms down as tight as possible, over-tightening can cause serious damage. Here’s why it’s bad news:
- It can deform the gasket, leading to leaks
- It puts unnecessary stress on the cam arms and locking mechanism
- It makes disconnection more difficult and potentially dangerous
To achieve the perfect fit:
- Connect the male and female parts
- Close the cam arms until you feel resistance
- Give a firm, but not excessive, final push to secure the connection
For consistent tightening, consider using a torque wrench designed for camlock fittings.
7. Size Matters: Picking the Right Camlock for the Job
Using the wrong size camlock fitting can lead to leaks, damage, and safety hazards. Here’s a quick guide to camlock sizing:
Size (inches) | Common Applications |
---|---|
1/2″ – 3/4″ | Small-scale fluid transfer, laboratories |
1″ – 2″ | Medium-duty industrial applications |
3″ – 6″ | Heavy-duty industrial and agricultural use |
Remember: Camlock sizes refer to the inner diameter of the fitting, not the outer diameter of the hose or pipe.
To ensure compatibility, always consult the manufacturer’s specifications and use fittings from reputable suppliers. Camlock Fitting Woes? Your Ultimate Troubleshooting Guide for Industrial Fluid Transfer.
Camlock Care 101: Keeping Your Fittings Fighting Fit
Proper maintenance is key to extending the life of your camlock fittings and preventing costly downtime. Here’s a maintenance schedule to keep your fittings in top shape:
Daily:
- Visually inspect fittings for damage or wear
- Clean off any debris or residue
- Check for proper operation of cam arms
Weekly:
- Perform a thorough cleaning with appropriate solvents
- Lubricate cam arms and locking mechanisms
- Test for leaks using low-pressure air or water
Monthly:
- Conduct a detailed inspection of all components
- Replace any worn gaskets or O-rings
- Check for signs of corrosion or material degradation
Annually:
- Perform a complete overhaul of all camlock fittings
- Replace any fittings showing significant wear or damage
- Review and update your maintenance procedures
When DIY Won’t Cut It: Knowing When to Call in the Pros
While many camlock fitting issues can be resolved with a bit of DIY know-how, some problems require professional attention. Here are some red flags that signal it’s time to call in the experts:
- Severe corrosion or pitting on sealing surfaces
- Bent or damaged cam arms that can’t be straightened
- Cracks or fractures in the fitting body
- Repeated leaks despite replacing gaskets and proper assembly
When seeking professional help, look for technicians certified in industrial fluid transfer systems. The initial cost may be higher, but it can save you money and headaches in the long run.
Camlock Crystal Ball: Future-proofing Your Fitting Game
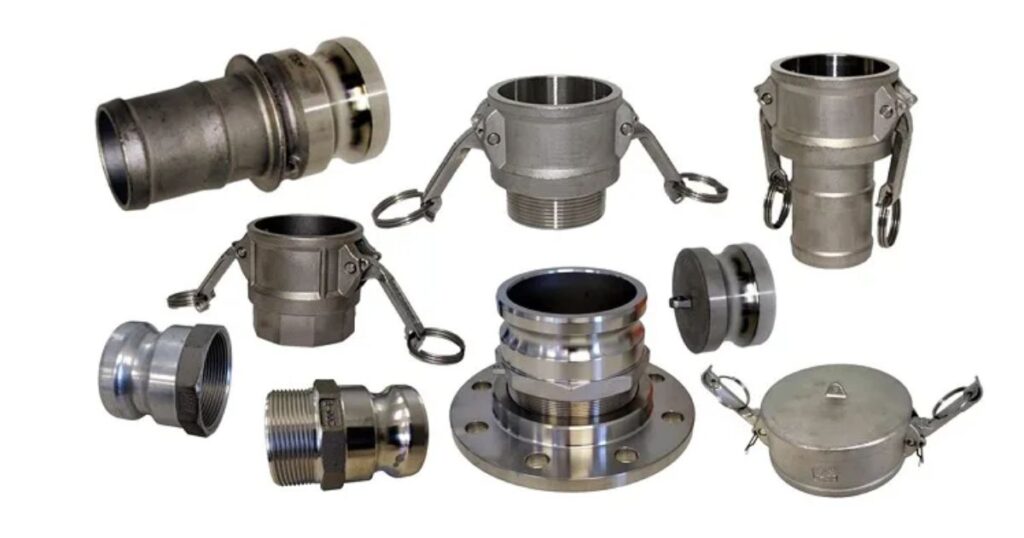
The world of industrial fluid transfer is constantly evolving. Stay ahead of the curve by keeping an eye on these emerging trends:
- Smart clocks: Fittings with integrated sensors to monitor pressure, temperature, and flow rates.
- Advanced materials: New alloys and composites offering improved durability and chemical resistance.
- Eco-friendly designs: Fittings optimized for reduced material usage and improved recyclability.
To future-proof your camlock fitting game:
- Attend industry trade shows and seminars
- Stay connected with reputable suppliers for product updates
- Consider piloting new technologies in non-critical applications
Wrapping It Up: Your Camlock Cheat Sheet
Let’s recap the key takeaways for mastering your camlock fitting challenges:
- Regular inspection and maintenance are crucial
- Choose the right material and size for your application
- Proper alignment and tightening prevent most issues
- Clean and store fittings correctly when not in use
- Don’t hesitate to seek professional help for complex problems
Remember, a well-maintained camlock fitting is the unsung hero of industrial fluid transfer. By following these tips and staying vigilant, you’ll keep your operations flowing smoothly and efficiently.
Conclusion
Camlock fittings may seem like simple components, but they play a critical role in industrial fluid transfer. By understanding common issues and implementing proper maintenance practices, you can significantly reduce downtime, prevent costly spills, and improve overall operational efficiency.
Remember, the key to camlock fitting mastery lies in prevention and proactive care. Regular inspections, proper usage, and timely repairs will keep your fittings operating at peak performance for years to come.
FAQs
- How often should I replace my camlock fittings?
With proper maintenance, quality camlock fittings can last 5-10 years. However, replace them immediately if you notice significant wear, damage, or repeated leaks. - Can I use camlock fittings for food-grade applications?
Yes, but ensure you choose fittings specifically designed for food-grade use, typically made from 316 stainless steel with food-safe gaskets. - What’s the difference between aluminum and stainless steel camlocks?
Aluminum is lighter and less expensive but less durable and corrosion-resistant than stainless steel. Stainless steel is preferred for harsh environments and critical applications. - Are camlock fittings suitable for high-pressure applications?
Standard camlock fittings are typically rated for pressures up to 250 PSI. For higher pressures, specialized high-pressure camlocks or alternative fitting types may be necessary. - How do I convert between NPT and camlock fittings?
Use a camlock x NPT adapter fitting. These are available in various sizes and materials to match your specific needs.